MORE THAN JUST RECYCLING?
Who doesn’t know it? Once the remote control or toy stops working, the empty batteries are replaced and thrown into the collection box or repurposed lunchbox. What is initially forgotten is dug out and returned for recycling on the next trip to a collection point. Batteries are recycled. It’s good for the environment and an integral part of our daily lives.
But what if the product isn’t a remote control but an electric car, with lithium-ion batteries ten times larger? How does it work then? Are so-called traction batteries also recycled at the end of their use to reduce the undesirable environmental impacts of battery production? Or are there other options to help achieve a circular economy for batteries?
„IMPLEMENTING A CIRCULAR ECONOMY FOR TRACTION BATTERIES MAXIMIZES RESOURCE EFFICIENCY, REDUCES ENVIRONMENTAL IMPACTS, AND PROMOTES A SUSTAINABLE BATTERY ECOSYSTEM.“
Batteries are considered a key technology for electrifying the mobility sector and are an important part of a more environmentally conscious future. For example, batteries can contribute to efficient resource utilization through maintenance and recycling-friendly design, or effective recycling and recovery strategies. Measures promoting circularity for batteries are diverse but always share the same core goal: closing battery material loops to maximize environmental and economic viability. To gain a comprehensive overview of promising levers, it’s worth examining the different life stages of a battery (see figure). It quickly becomes clear: Compared to our home batteries, a circular economy for traction batteries is more than just recycling! Let’s look at the different life stages and possibilities for traction batteries in a circular economy.
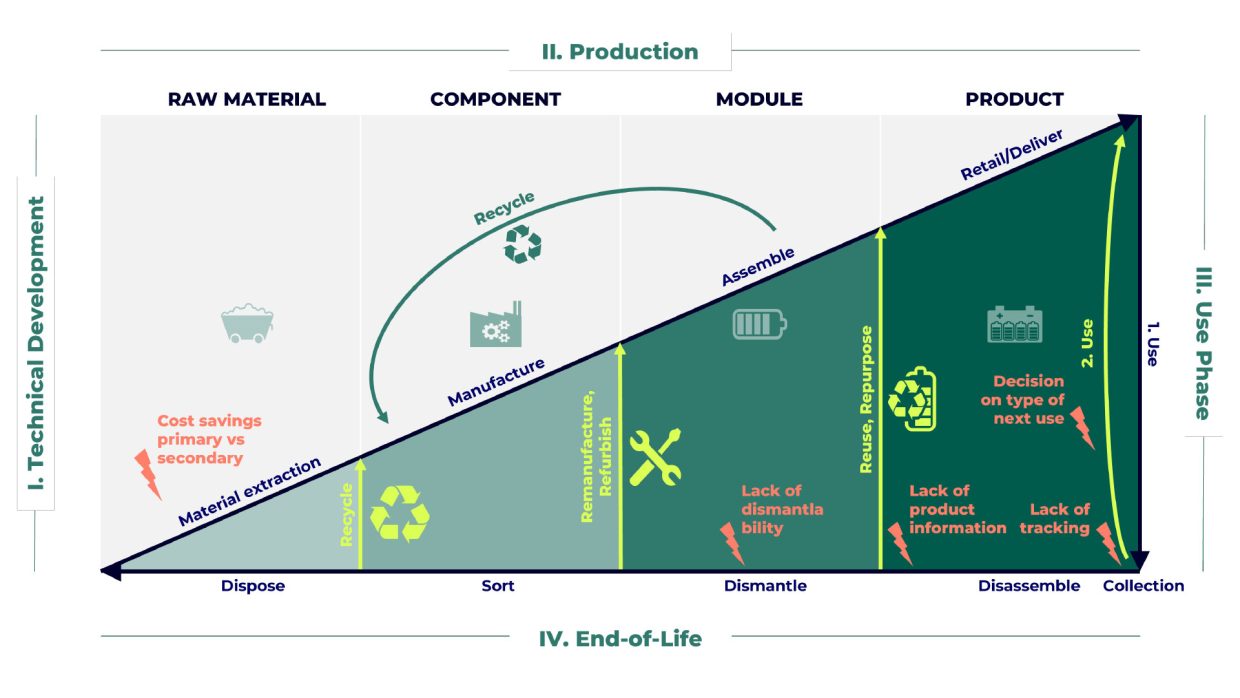
FIGURE: TRACTION BATTERIES IN A CIRCULAR ECONOMY WITH MEASURES OVER THE ENTIRE LIFE CYCLE.
I. Technical Development:
- Application of eco-design principles (Design for Circularity) to ensure recyclability and easy disassembly.
- Improvement of energy density and lifespan to extend the battery’s usage phase.
- Promotion of standardized battery components to facilitate repair and refurbishment.
Deep Dive „Design for Circularity”
Design for Circularity encompasses crucial strategies that influence the various phases of resource utilization and waste management in a circular economy. Originally known as the ‘6 Rs’ of the circular economy, today up to 10 different strategies are distinguished: Refuse, Rethink, Reduce, Reuse, Repair, Refurbish, Remanufacture, Repurpose, Recycle, and Recover. Each circular strategy contributes to preserving and recovering the value of our limited resources.
II. Production:
- Minimize waste generation and implement closed-loop material recovery systems.
III. Use Phase:
- Promotion of responsible consumption behavior to extend battery lifespan.
- Development of smart charging and usage strategies to optimize battery performance and utilization.
- Promotion of energy storage solutions enabling demand response and grid stabilization.
IV. End-of-Life (EOL):
- Establishment of efficient collection and recycling systems, including take-back and producer responsibility programs for battery recovery.
- Encouragement of consumers to return used batteries to designated collection points.
- Possibility of reusing batteries or their components in a different application context (Second-Life), e.g., in stationary energy storage systems or electric vehicle charging stations.
- Overhauling used batteries to a nearly new condition and reintroducing them to the market (Remanufacturing).
- Improving and renewing used batteries, e.g., by replacing control elements and modules, to extend their lifespan and enhance efficiency (Refurbishment).
- Reusing battery materials as secondary material, which is used instead of primary material for manufacturing new batteries (Recycling).
“WITHIN A CIRCULAR ECONOMY, COMPLEX GOAL CONFLICTS CAN ARISE, DELAYING THE ACHIEVEMENT OF A CIRCULAR ECONOMY.”
Cost savings Primary vs. Secondary materials:
The production of new batteries from primary raw materials can initially be cheaper than from secondary raw materials. However, hardly anyone wants to buy a significantly more expensive car just because it’s made from recycled materials. The challenge is to strike a balance between the short-term costs of primary materials and the long-term benefits of a sustainable circular economy.
Decision on reuse type:
Should valuable resources be directly recycled into new batteries? Or is it better to choose a simpler solution like Second-Life or Refurbishment? This question confronts decision-makers when deciding on the reuse type of batteries. Similarly, it is questionable to what extent a long battery lifespan should be aimed for. While this achieves positive effects on the profitability of the original investments, longer lifespans delay the availability of secondary raw materials as batteries stay in use longer.
Lack of disassembly:
Many existing products on the market lack disassembly for EOL applications. While vehicle manufacturers focus on achieving optimal battery performance for their electric vehicles, increasing complex design makes both disassembly and recycling more challenging. Therefore, EOL managers (dismantling companies and recyclers) increasingly face the challenge of balancing business or technically optimized performance with the desired implementation of Design for Circularity strategies.
Lack of traceability/Lack of product information:
For optimized recycling processes and high-quality second-life applications, all stakeholders involved need dynamic and accurate data on battery performance and condition at the end of their lifespan. For this, the necessary data must be collected, stored, and provided uniformly and as seamlessly as possible. A premise that we are still far from today. For the future, it is crucial to develop a balanced approach that respects the information needs while implementing protection mechanisms for intellectual property and data. Only then can the efficiency and sustainability of the battery recycling process be maximized.
“A DIGITAL PRODUCT PASSPORT (DPP) CAN SUPPORT OPTIMIZING A PRODUCT/BATTERY TOWARDS A CIRCULAR ECONOMY AND RESOLVING GOAL CONFLICTS.”
The EU has set out to ensure greater transparency through digitally stored information. In December 2023, the EU institutions reached a provisional agreement on the provisions of the ‘Ecodesign for Sustainable Products Directive,’ which aims to tighten the existing ‘Ecodesign Directive.’ Already in August 2023, the ‘New EU Batteries Regulation’ came into force, specifically regulating the ESG impacts of batteries. Both proposals lay the groundwork for the introduction of a DPP.
A DPP – or Battery Passport – is an electronic record containing all relevant information about the entire lifecycle of a product or battery. This includes material composition, recycling rates, origin, procurement records, product characteristics, safety requirements, and environmental impacts such as CO2 emissions. The aim of the DPP is to improve transparency and traceability and to make all relevant information accessible and barrier-free for stakeholders in the value chain. This facilitates the implementation of circular economy measures, such as data-driven product optimizations in line with ecodesign principles and contributes to resolving the aforementioned goal conflicts.
„THROUGH THE STRATEGIC PARTNERSHIP WITH CIRCULARISE, P3 OFFERS A UNIFIED SOLUTION FOR FULL TRANSPARENCY OF THE SUPPLY CHAIN AND COMPLIANCE WITH CURRENT AND FUTURE REGULATIONS.“
P3 offers holistic approaches to support the implementation of a circular economy. P3 relies on numerous Life Cycle Assessments (LCAs) to determine the CO2 and environmental footprint of products, which is essential for complete documentation in the DPP.
Furthermore, P3 collaborates with the DPP provider Circularise (Quick Link), a leading provider of Battery Passports. The aim of this partnership is to revolutionize the battery and automotive industries by offering a unified solution for full transparency of the battery supply chain. Circularise brings unique expertise in the field of Battery Passport technology, while P3 has over two decades of experience in strategic consulting for OEMs. This accelerates the establishment of a robust infrastructure for DPPs, which forms the basis for a successful circular economy in the battery and automotive industries. This way, we will be able to holistically utilize and manage not only household batteries but also traction batteries in the future.