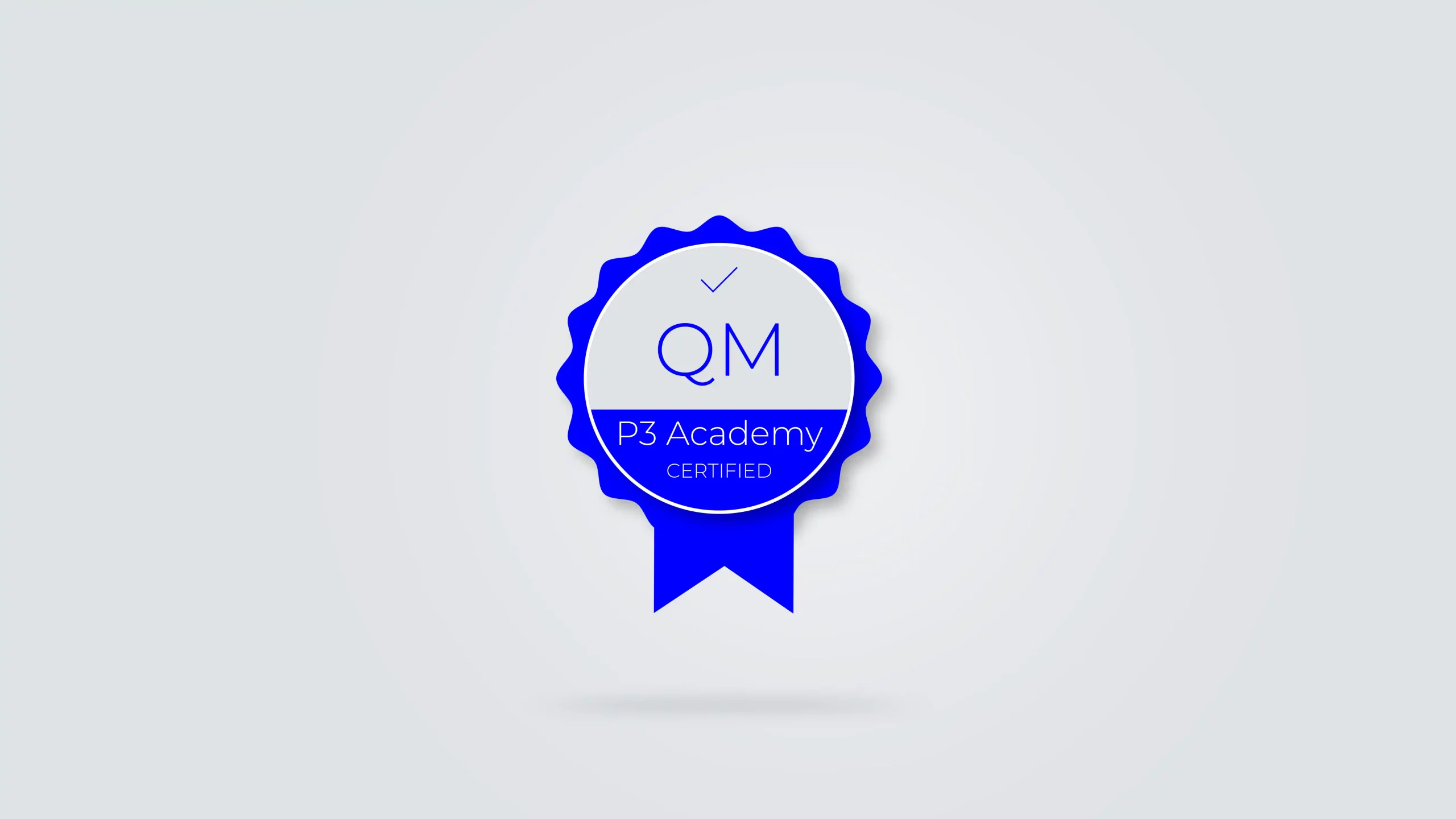
Your Motivation
There is a desire to
- Improve the quality of products and processes
- Identify the key variables that influence performance
- Identify the service design parameters
- Minimize the response time to customer complaints
- Shorten the service delivery time to customers
- Reduce quality costs due to rework and incorrect information leading to wrong decisions
General Learning Objectives
- Understanding and applying the concept of the “robust process”
- Reduce the likelihood of PPM by reducing process variation
- Reduce the cost of material, process and product controls
Main Focus
Quality technique
- Methodology: The Taguchi approach
- Parameter design
- Signal / noise analysis
Loss function
- Applications / loss function for series / exercises
Planning of experiments
- Methods of experimental design / Orthogonal matrices
- Analysis of results / Selection of optimal conditions
Regular analysis
- Exercises & practical workshop
Interpretation of the parameters
- Exercises & practical workshop
Target Group
Regardless of your experience, you are welcome to attend this course. There are no special requirements.
The training is relevant for the following target groups, among others:
- Process engineers
- Technicians
- Six Sigma Black Belts
Further Information
- Participants: <10
- Languages: English, Spanish
- Mode: Onsite, remote
- Pedagogy: Training enriched with real-life examples and exercises
- Assessment: Based on participant interaction and final assessment
Tools implemented:
- Robust design
- Orthogonal arrays
- Signal-to-noise ratio
UPCOMING TRAININGS
16
- July
- MUNICH, ONSITE
- 09:00 AM - 05:00 PM
As an official training partner of GPM, we look forward to your participation!
01 - 02
- September
- ONSITE, STUTTGART
- 09:00 AM - 05:00 PM
04 - 05
- September
- REMOTE
- 09:00am - 05:00pm
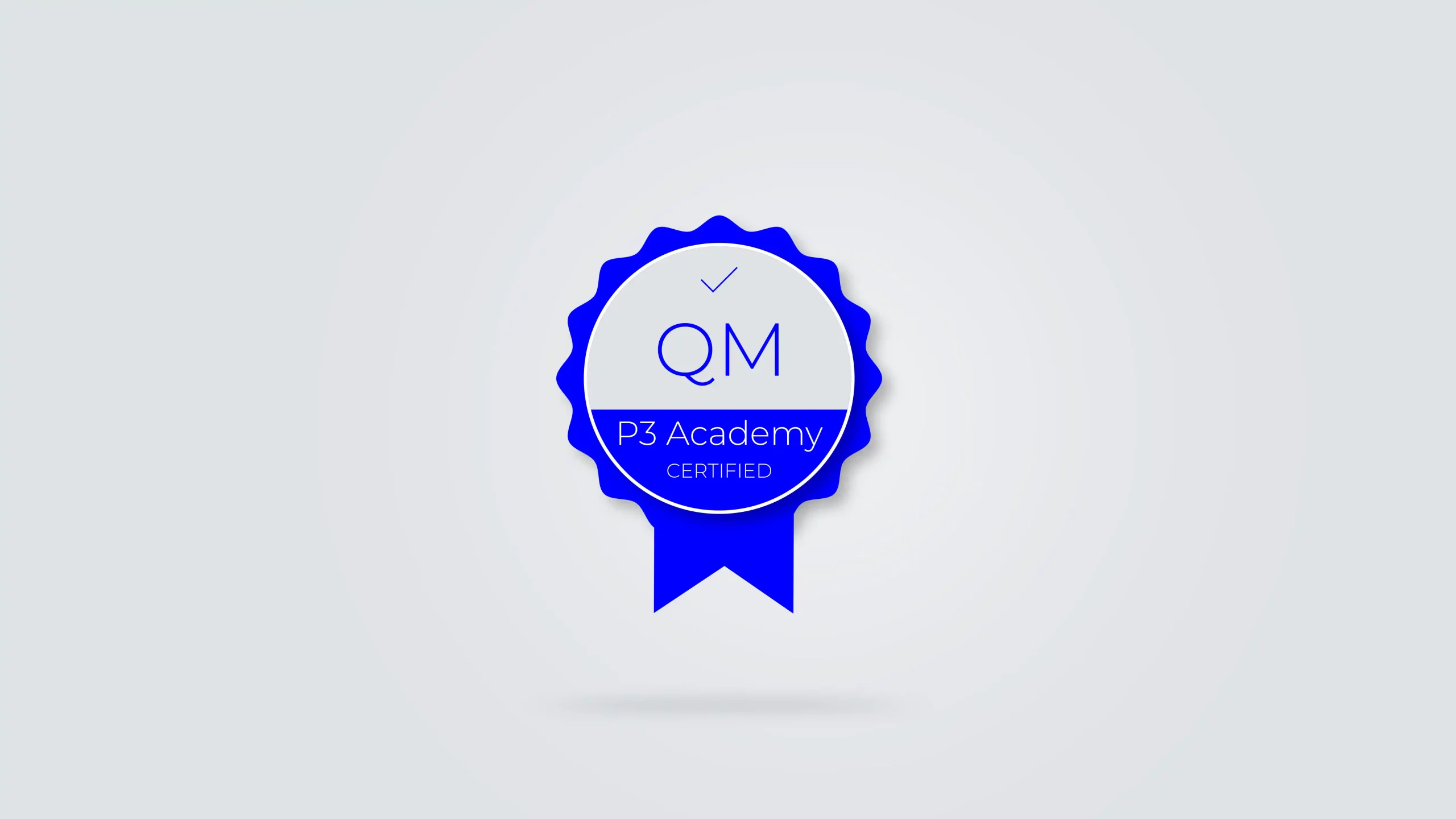
Your Motivation
There is a desire to
- Improve the quality of products and processes
- Identify the key variables that influence performance
- Identify the service design parameters
- Minimize the response time to customer complaints
- Shorten the service delivery time to customers
- Reduce quality costs due to rework and incorrect information leading to wrong decision
General Learning Objectives
- Understanding and applying the concept of the “robust process”
- Reduce the likelihood of PPM by reducing process variation
- Reduce the cost of material, process and product controls
MAin Focus
Quality technique
- Methodology: The Taguchi approach
- Parameter design
- Signal / noise analysis
Loss function
- Applications / loss function for series / exercises
Planning of experiments
- Methods of experimental design / Orthogonal matrices
- Analysis of results / Selection of optimal conditions
Regular analysis
- Exercises & practical workshop
Interpretation of the parameters
- Exercises & practical workshop
Target Group
Regardless of your experience, you are welcome to attend this course. There are no special requirements.
The training is relevant for the following target groups, among others:
- Process engineers
- Technicians
- Six Sigma Black Belts
Further Information
- Participants: <10
- Languages: English, Spanish
- Mode: Onsite, remote
- Pedagogy: Training enriched with real-life examples and exercises
- Assessment: Based on participant interaction and final assessment
Tools implemented:
- Robust design
- Orthogonal arrays
- Signal-to-noise ratio
Upcoming Trainings
16
- July
- MUNICH, ONSITE
- 09:00 AM - 05:00 PM
As an official training partner of GPM, we look forward to your participation!
01 - 02
- September
- ONSITE, STUTTGART
- 09:00 AM - 05:00 PM
04 - 05
- September
- REMOTE
- 09:00am - 05:00pm